伴随着鸣笛警报和隆隆声响,10余米的高空上一台大型行车正缓缓运行至机车上方,随着中修机车7712的核心部件柴油机发电机组顺利吊装引入就位,标志着铁运处第二台中修机车检修进入了尾声。
抓攻关、促创新、降成本……今年以来,铁运处从源头控制、设备管理、修旧利废等多维度入手,深挖增效潜能,提升生产质效。随着一项项技术攻关成果转化、一个个自主创新课题落地、一笔笔节支数据不断刷新,不断为企业高质量发展注入了持续动能。
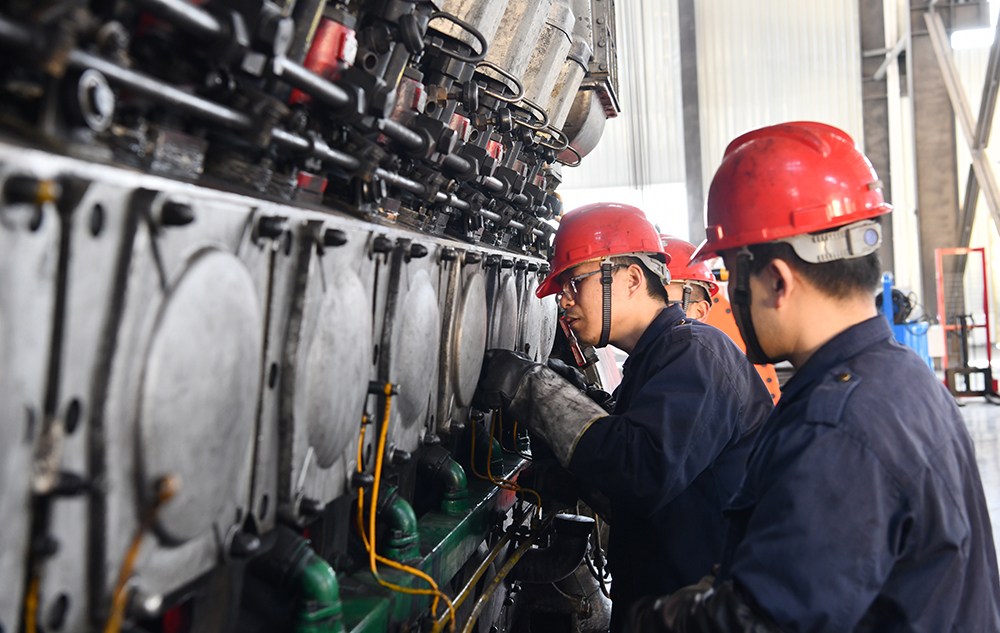
“无论如何都要啃下这块‘硬骨头’”
年初,随着机车大中修库的投入使用,铁运处立足生产实际,强化问题导向,集中专业力量开展攻关,努力把成本降到最低。
他们认真梳理典型机车故障,如何完成机车弹性联轴节更换工作是摆在他们面前的一道难题,如果继续通过外委维修,更换一次就需要3万元的费用,不仅维修周期长,而且费用高昂。
“前方既然没有路,那我们就自己摸索着走出一条新路,无论如何都要啃下这块‘硬骨头’。”遇难不畏难,今年年初,检修车间副主任顾勇牵头成立了此项技术的攻关小组,并立下了“军令状”。收集数据、归类整理、研究分析……经过不断的分析研判,他们找到了“病灶”所在,“对症试药”,先后提出4个技术方案,并马不停蹄地在运用机车上逐一跟踪对比试验。
功夫不负有心人,经过反复测试验证,技术攻关小组彻底解决了机车运行中弹联甩油的技术难题,不仅节约了费用,也为柴油机分解组装、配气相位的调整、弹联更换、缸套快速安装、泵支撑箱齿隙调整、空压机检修磨合试验等类似关键检修工艺提供了新思路。
“50万元是怎么节省的?就是靠咱们职工这样一点一滴修出来的”
“这台机车更换下来的16个气缸套,通过焊修、打磨、耐压试验等自主检修,可以实现7个气缸套的复用,一台机车就能节约成本近2万元,这得益于主动的‘走出去’的结果。”正在检修气缸套的机车维修工杨印虎说。
积极“走出去”开阔视野,主动“学回来”促进成果转化应用,不断提升自主修能力,是机车简易中修提质增效的又一实招。去年10月,在建设机车简易大中修库的同时,铁运处分两批次派送职工前往平顶山铁运处机务段进行为期一个月的业务学习,通过交流互鉴,对标找差、取长补短。在外出学习的同时,他们对委外修项目充分调研论证,研发实用维修流程,突破技术瓶颈,逐步扩大自主修范围。
“目前,我们已实现了解体、清洗、检修、组装、调试、试运等上千道工序的完全自主维修,之前外委中修费用平均每台为123万元,现在去掉材料和配件费用73万元,50万元是怎么节省的?就是靠咱们职工这样一点一滴修出来的。”机务段段长王胜在现场跟笔者算起了“节约账”。
“创新不分大小,优于以往、解决问题都是创新”
在机车拆卸维修过程中,配件大多都很沉重,为最大限度的减少职工劳动作业强度,提高作业功效,该处积极鼓励职工利用小发明、小创造解决身边的作业难题。
袁冲是检修车间的副主任,“创新不分大小,优于以往、解决问题都是创新”是他经常跟同事们说的话。
活塞连杆拆装保养就是一项费时费力的作业,检修车间副主任袁冲看在眼里、急在心上。他跟工友们一起仔细观察作业过程,反复研究解决方案。画图纸、搞设计,袁冲和工友们用了一周时间就制作出了内燃机车活塞连杆组装配工作台,彻底解决了活塞连杆拆装过程中的取送困难问题,避免了可能发生的安全风险。
他不光自己解决问题,他还带动大伙儿一起搞研究、搞发明。今年以来,他们根据机车检修作业中拆解、测量、检测等需求,先后制作了联合调节器拆装翻转架、喷油器除炭设备、气缸套耐压试验装置、燃油泵油封改造、冷却单节打压装置等20多项小改小革、小发明,用科技创新为该处高质量发展贡献了动力与保障。
(审核:尹良功 责编:尹杰)